Pcb proofing, small and medium batch production
PCB circuit board production process
Cutting - inner layer graphics - lamination - drilling - electroplating - outer layer - solder mask - surface treatment - forming - electrical testing - FQC - FQA - packaging - finished product
Layer pressure
According to the requirements of MI, the inner core board and the PP sheet are stacked and fixed, and the inner core board and the PP sheet are combined under a certain temperature, pressure and time condition according to the process pressing parameters, and are pressed into a complete multilayer PCB. board.
Production process:
Browning - rivets - pre-discharge - stacking - hot pressing - cold pressing - stripping - X-RAY drilling - edge - the next process
A, browning
The purpose of browning is to increase the roughness of the surface of the copper foil and increase the contact area with the resin, which is advantageous for the resin to be sufficiently diffused and filled.
B, hot pressing, cold pressing:
Hot pressing
The plate pressed by the hot press is transported to the cold press by the transport vehicle, and the purpose is to gradually lower the temperature inside the plate under the action of the cooling water to better release the internal stress in the plate and prevent the plate from being bent.
C, remove the board:
The cold-pressed board is manually removed by a person. When the board is removed, the production board and the steel plate are respectively separated by paper sheets to prevent rubbing.
![China Hardware Business Network]()
![China Hardware Business Network]()
![China Hardware Business Network]()
Drill hole
Use the drill on the rig to drill the required holes in the board at high and falling speeds.
Production process:
To board - drill positioning hole - upper plate - input data - drilling - first board inspection - red film - polishing peak - the next process
A, the role of drilling:
Drilling of circuit boards is suitable for component soldering, assembly and layer-to-layer conduction of circuit boards.
B, the role of aluminum sheet:
The aluminum sheet acts as a heat conduction in the drilling process; the positioning acts as a position; the effect of the peak of the aperture is reduced and the surface scratch is prevented.
C, polishing the peak:
When drilling, due to the different materials of the plates, there is a peak at the edge of the hole. After drilling, the hole should be polished with a manual sander.
D, red film:
When drilling the first plate of the drill, drill it together with the red film, and then use the hole point film to check whether the first plate of the drill hole has the problem of boring and missing drill. The first board is qualified. The red film can be used to check whether the batch production board has drilled. And missing drill problems.
![China Hardware Business Network]()
![China Hardware Business Network]()
Http://news.chinawj.com.cn
![Interpretation of the process principle of each production process of PCB board - lamination, drilling]()
Editor: (Hardware Business Network Information Center) http://news.chinawj.com.cn
Elevator LOP
We produce LOP for all major elevator and escalator brands for OTIS Elevators, ThyssenKrupp Elevators, Schindler Elevators, KONE Elevators, Mitsubishi Elevators, Fujitec Elevators, Hitachi Elevators, Toshiba Elevators, Fuji Elevators, Express Elevators, Sigma Elevators, LG Elevators, Hyundai Elevators, BLT Elevators, CANNY Elevators, SJEC Elevators, KOYO Elevators.
We have LOP with bottom box and LOP without bottom box to choose from.
The LOP without the bottom box is wall-mounted, because it is easy to install, many customers like to choose this style.
Our LOP also has many different sizes, the length can be selected from 325mm to 500mm, and the width is from 90mm to 205mm (Duplex LOP).
The material of the panel can be selected: hairline stainless steel, mirror stainless steel, titanium alloy hairline, titanium alloy mirror, tempered glass, etc.
There are also many options for matching display panels: red dot matrix display, black and white segment code display, blue LCD display, TFT display, etc.
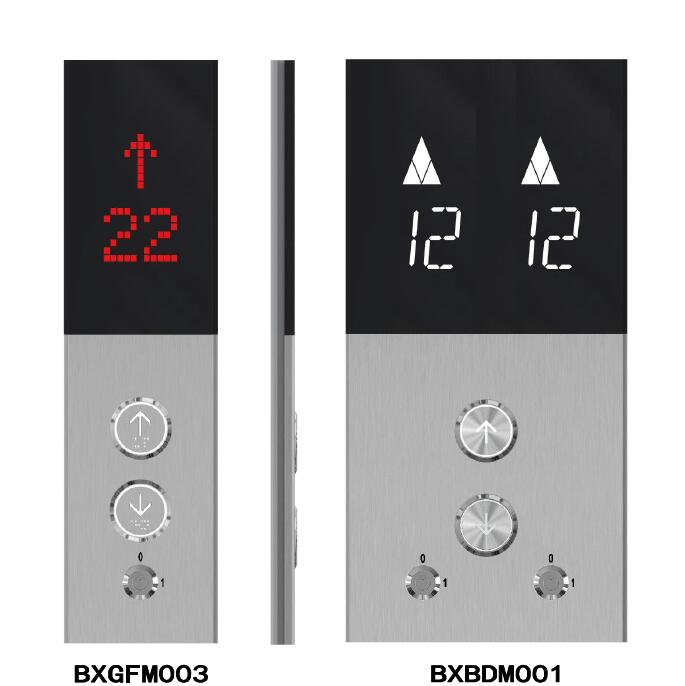
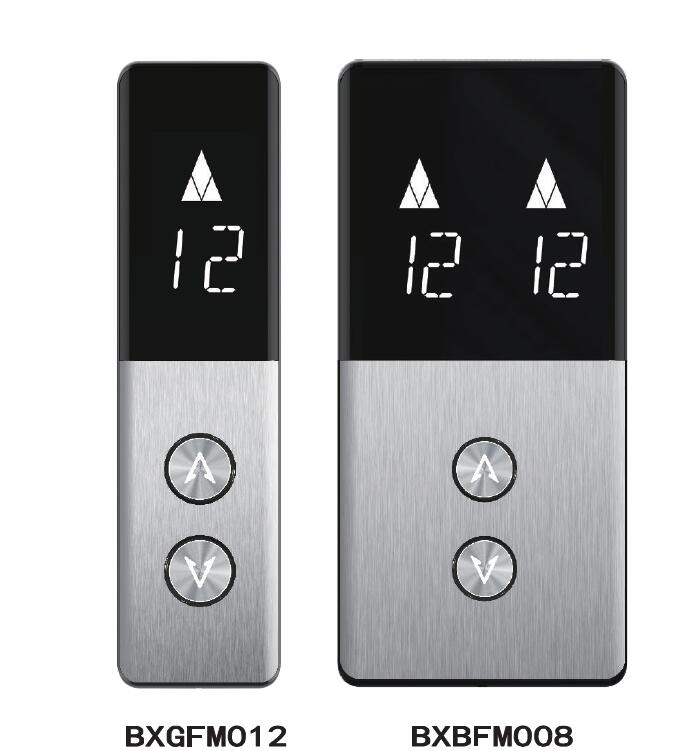
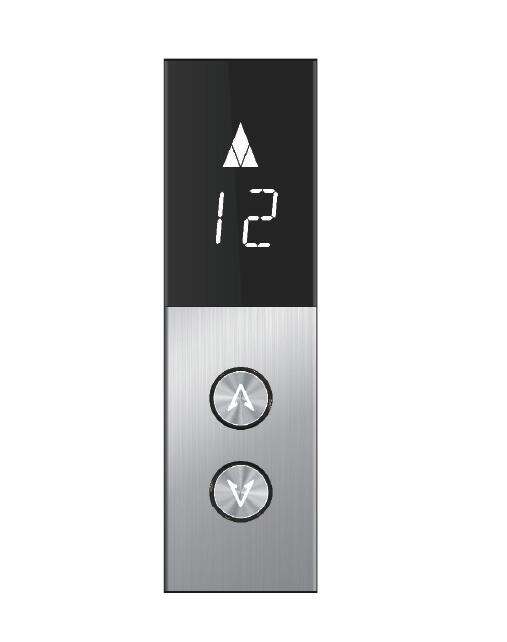
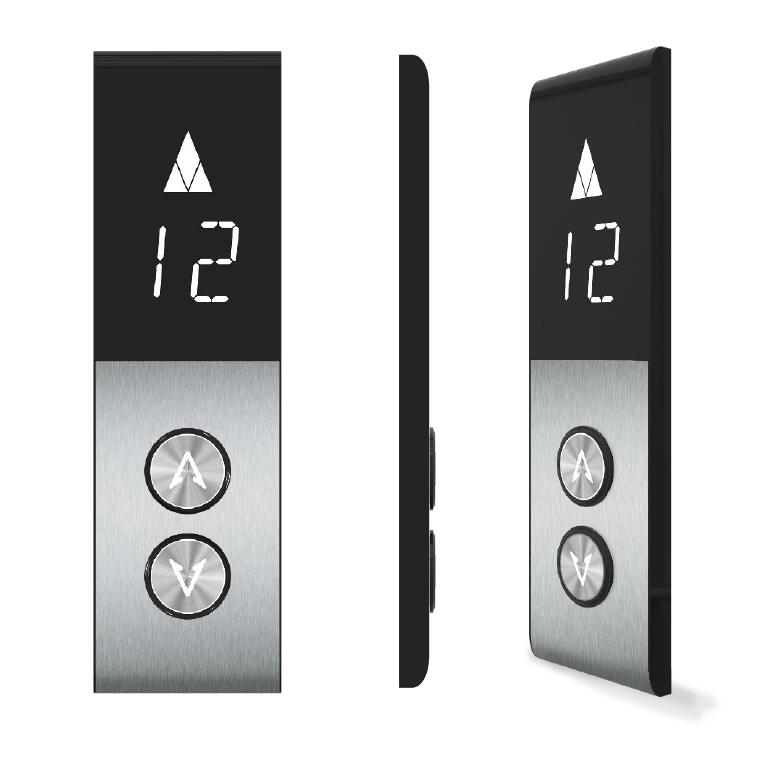
Elevator LOP,Passenger Elevator LOP,Lift LOP,Elevator Landing Operating Panel,Simplex Operation Elevator LOP With Dot Matrix Display
Suzhou Keffran Parts Co.,ltd , https://www.keffran-elevatorsmart.com