As a precision measuring instrument, the coordinate measuring instrument is very important, and it depends on the three-coordinate measuring instrument itself. Only a good three-coordinate measuring instrument can ensure its accuracy. Therefore, the selection of a suitable coordinate measuring machine is the key to the use of each project.
ZEISS Industrial Measurement is the world's leading manufacturer of three-coordinate measurements and the inventor and founder of three-coordinate measurement technology, dedicated to providing professional measurement solutions for multi-dimensional measurement needs in industrial manufacturing and measurement laboratories. Therefore, even in the aerospace industry where accuracy is extremely demanding, ZEISS products are common.
When the micrometer is not accurate enough
When the European Space Agency (ESA) is preparing for a space probe (see Figure 1), the most important task is to achieve the ultimate in precision. As Europe's first Mercury program, the detector will experience very harsh environmental changes during the six-year exploration of the universe. Therefore, all components must meet special high requirements. LT Ultra Precision Technology Co., Ltd. won this important order by using Zeiss measurement technology.
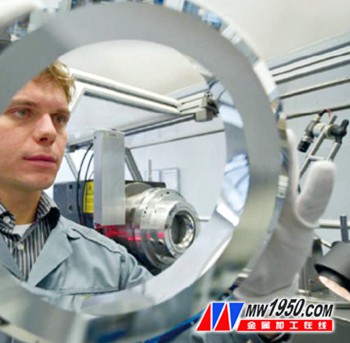
LT Ultra is the world's leading manufacturer of high performance metal optics, ultra precision equipment, air bearing components and laser beam guiding assemblies. As the accuracy requirements of the project became higher and higher, they found that only accurate machining is not enough. “Our production equipment is becoming more and more sophisticated. Measurement technology must also be synchronized,†said Richard Wideman, President of LT Ultra. For this reason, the company purchased the PRISMO ultra measuring machine from Zeiss. In the past, LT Ultra relied heavily on equipment from external service providers for many of the most demanding measurements. Since it is often impossible to complete various tasks as required, the work schedule has been greatly slowed down, resulting in many projects failing to be carried out on time. For the company, in order to obtain orders from the European Aviation Authority, the PRISMO ultra measuring machine (see Figure 2) is very necessary.
In order to meet the accuracy of the Mercury program less than 250nm, Zeiss has configured the company with RISMO ultra. Each of its components has been carefully selected and carefully assembled, and every detail has been carefully considered so that PRISMO ultra can fully meet these high precision requirements. In addition, Zeiss modified the software settings for this special work, ensuring that the stylus is only slightly touching the workpiece, ensuring that it does not damage its sensitive surface.
Confidence comes from quality assurance
The manufacturing industry has undergone tremendous changes in the past 40 years. Jamco Aerospace has a deep understanding of these changes, and they realize how important it is to keep advanced quality testing equipment into their manufacturing processes to maintain their competitiveness! So Jamco introduced two scanning coordinate measuring machines from Zeiss Industrial to ensure the accuracy of each step in the manufacturing process.
Jamco is a manufacturer known for manufacturing complex, structural components for the aerospace industry. 95% of the company's orders come from the aerospace industry, and the remaining 5% come from the land transportation industry. They are a factory that has been committed to providing comprehensive machining services and airframe facilities. Some of the major clients include: Northrop Grumman, Boeing, Spilit Space Systems, and the US government.
In order to maintain the company's industry competitiveness, after in-depth research, Jamco determined that Zeiss's CONTURA G2 10/21/6VAST XXT RDS with scanning technology (see Figure 3) is best suited for their testing. CONTURA G2 10/21/6 is a powerful device that meets the size of their parts. Designed for small, multi-angled parts, the VAST XXT RDS Rotary Probe measures at 20 to 736 different angles with a 2.5° step angle. Compared with the previous triggered coordinate measuring instrument, this scanning technology can get more information in a shorter time. Through this, the efficiency is improved, and the manufacturing cost is also reduced. And in order to facilitate the more efficient handling of larger aerospace components such as cofferdams, stringers, ribs, webs and frames, the same CALYPSO software and ZEISS quality are required. They purchased a large gantry CMM, an MMZ 20/50/15, which not only measures larger parts, but also measures smaller parts in large quantities.
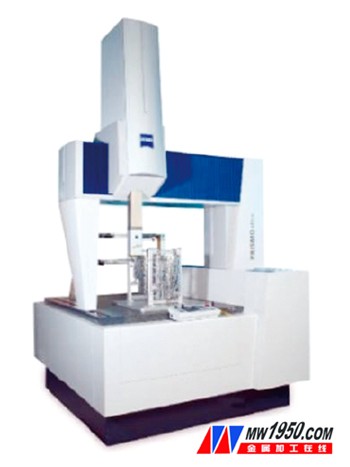
Jamco is also very impressed with the ease of use and compatibility of the CALYPSO software. “Even if the operator is not sure how to set up a part, it does not matter, the software will display multiple part views to make this setup process easier,†said Ronald Lee, Quality Control Manager at Jamco.
The quality assurance of the Zeiss system runs through all of Jamco's manufacturing processes and brings new confidence to Jamco and its customers.
Higher precision and more power
Mr. Stefano Pradolin, Manager of Maintenance and Automation at Pietro Rosa, said: “We are very proud to use Zeiss' measurement system, which means quality and precisionâ€, “These machines have greatly improved our measurement resultsâ€. Pietro Rosa is one of the leading manufacturers of turbines and compressor blades for the aerospace industry and for the oil, gas and marine industries. Parts made by Pietro Rosa vary in size, with blade sizes as small as 35mm and as large as 1.7m. However, regardless of the size of the parts, one thing is the same: the importance of quality inspection is directly proportional to its complexity.
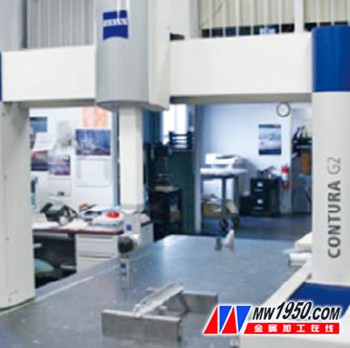
Inside the power generating turbine, the shape and size of the turbine blades largely determine the amount of electricity generated, so the dimensional inspection of the blades is extremely important. They include surfaces of any shape and can only be checked by scanning. The base of the blade, that is, the root is very narrow, and the tolerance here is generally large, at 2/10 or 3/10 mm. The cylindrical, flat or conical dimensions are relatively easy to measure, but the tolerance requirements are very strict, at 1/100 or 2/100mm, ie 10-20mm. Measurement tolerances of up to 1 mm can only be detected using a measuring instrument. Figure 4 shows the ZEISS ACURRA coordinate measuring machine.
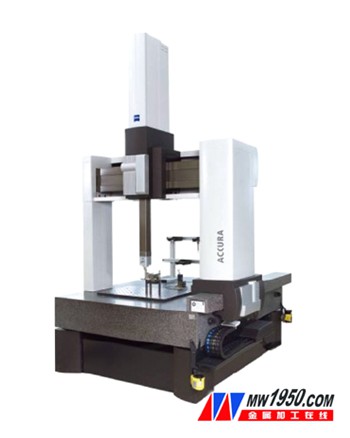
Since 1996, Pietro Rosa has trusted ZEISS measurement technology. At that time, Zeiss' UMC 850 was the only measuring instrument on the market with active scanning technology. It measures the measurement of an object by continuous scanning, rather than measuring it point by point with a probe. For Pietro Roas, this was the only way to measure the surface of any blade of a turbine. Therefore, Pradolin never regretted his decision to purchase Zeiss instruments. “We were very satisfied from the beginning. Since the conversion of the equipment, there has not been a quality problem between us and our customers.†There is another factor that gives him confidence in Zeiss: “Zeiss has continuously enhanced its measurement technology and measuring instruments in recent years. And software always maintains the most advanced technology. For this reason, Pietro Rosa has invested in new systems for the past 15 years. The company currently has nine measuring instruments in operation.
Pradolin believes that market demand is the driving force behind the purchase of new gauges: “Customers want us to present more and more measurements. Therefore, we must improve our quality inspection capabilities and production capabilities.â€
Conclusion
The development of various industries has accelerated the pace of product update, and the requirements for the accuracy and speed of product inspection are getting higher and higher. It is believed that the coordinate measuring instrument will be more widely used in the measurement field. With its 90-year history and 42 years of CMM production experience, Zeiss will continue to provide customers with better measurement solutions.
Air Release Valve
Reliable Air Release Valve, Air Safety valves, Air Valve For Pipeline, Air Relief Valve, choose the high quality Air Release Valve For Pipelines.
Air Release Valve, Air Safety valves, Air Valve For Pipeline, Air Relief Valve
Zhejiang Philic Fluid Control Co.,LTD , https://www.philicflow.com