Digital truck scale large scale body installation:
Digital Truck scale body installation requirements, as a general analog truck installation requirements, but also need to do a reliable basis flat, good contact sensor and the weighing platform, the force sensor relative to each other uniformly.
Digital truck scale correction
When all the previous work is completed, it is possible to start correction of the corner difference of the digital truck scale. Before correcting the angle difference, it is recommended to perform a simple calibration on the instrument before starting the pressure angle and adjusting the angle difference. General digital truck scales provide both manual and automatic correction methods for corner angles, and which methods are all dependent on personal habits. The author proposes that it is better to automatically correct the angle difference first, and then fine-adjust the correction manually, so that a very satisfactory correction result can be finally obtained.
After the corner difference correction is completed, calibration and other measurement performance tests can be started symmetrically.
Individual users will have such an erroneous view: Considering that digital truck scales are performed digitally and the range of adjustment is extremely large, it is not strictly necessary to force each digital sensor to be evenly distributed. Digital truck scale digital adjustment angle difference range is indeed very large, regardless of the sensor force difference is greater, can be corrected; but field experience shows that the results of such debugging are temporary, after a period of time, the angle difference Both linear and linear changes occur more severely, leading to poorer measurement accuracy. At the same time, we found that the accuracy of the digital angle correction is also not ideal in the case of uneven sensor forces.
Generally, after we install a digital truck scale, we should first set the relevant parameters of the sensor (including the sensor type, quantity, and sensors corresponding to each corner) on the instrument, and perform a simple calibration on the scale. Then use the weight as close as possible to the full scale (for example, the car loading weight) to press back and forth 2 to 6 times on the weighing platform to ensure that all parts of the weighing platform are stable and the sensor is subjected to vertical force. After weighing, you should be able to see the scale platform is reliably zeroed when it is pressed on the empty scale. Otherwise, check if there is a problem with the scale platform and the sensor. If there is any problem with the foundation, etc., solve the problem and then press the scale platform 2 or 3 times. , Check the balance back to zero.
When the entire scale body is returned to zero, the force status of the sensor is initially evaluated by looking at the code value output by each sensor when the empty scale is used. We use the following example to briefly explain the following evaluation methods.
For example: a digital truck scale body, a total of eight digital sensors installed, addresses are 1 to 8, respectively, distributed in the eight corners (ie installation location evaluation method: in the empty scale state to see the angle The inner code of the sensor meets the following three conditions, indicating that the weighing platform is well installed and the force of the sensor is relatively uniform:
1) The difference between the five inner codes of angular positions one and eight, two and seven, three and six and angular four and angular positions is not very large (experience: the difference is within 20%, the smaller the better).
2) The difference between the inner codes of angles 1, 4, 5, and 8 is not large, and the difference between the inner codes of angles 2, 3, 6, and 7 is not large (experience value: the difference is within 20%, the smaller The better.)
3) The code values ​​of the second, third, sixth, and seventh angles are approximately twice as large as the one, four, five, and eight code angles. s
The above-described exemplary methods and principles are equally applicable to digital truck scales with 4 and 6 or more digital sensors.
The installation of digital sensors is also arranged as regularly as possible in the address sequence, which will provide a lot of convenience for the adjustment of the back corners.
Digital truck scale correction
When all the previous work is completed, it is possible to start correction of the corner difference of the digital truck scale. Before correcting the angle difference, it is recommended to perform a simple calibration on the instrument before starting the pressure angle and adjusting the angle difference. General digital truck scales provide both manual and automatic correction methods for corner angles, and which methods are all dependent on personal habits. The author proposes that it is better to automatically correct the angle difference first, and then fine-adjust the correction manually, so that a very satisfactory correction result can be finally obtained.
After the corner difference correction is completed, calibration and other measurement performance tests can be started symmetrically.
Conclusion
The digital weighing system is an emerging weighing technology and is also a direction for the future development of weighing technology. It is being accepted and loved by more and more people with its many advantages and advantages. Digital truck scale is one of the most representative products in digital weighing systems. Through a brief introduction to its installation and debugging methods, we can easily find that the installation and commissioning of digital weighing systems are unique. Locally, there are many similarities with common analog weighing systems.
Electronic Scales (Shanghai Electronic Scales) Floor Scales (Small Scales) Large Platform Scales (Electronic Scales) Crane Scales (Shanghai Crane Scales)
Clamp Grow Light
We have many models clamp Led Plant Light, 1/2/3/4 head, circle model, bar model, and another model clamp Full Spectrum Led Lights. Easy installed, you can clip on everythere, works well for home depot, vegetables, hydroponic growth.
LED Grow Light Benefits:
|
More efficient: 100% of the power input for our LED grow lights is used for your plant chlorophyll production.
|
Better for environment: It saves 50% to 90% in energy consumption compared to incandescent bulbs or fluorescent tubes.
|
Less Heat: Low heated LED bulbs will protect your plants well.
|
Less trouble: No ballast to burn out likes other plant lights
|
No maintenance costs and 50,000 hours lifetime
|
Easy to install and use, plugging into the electric outlet directly
|
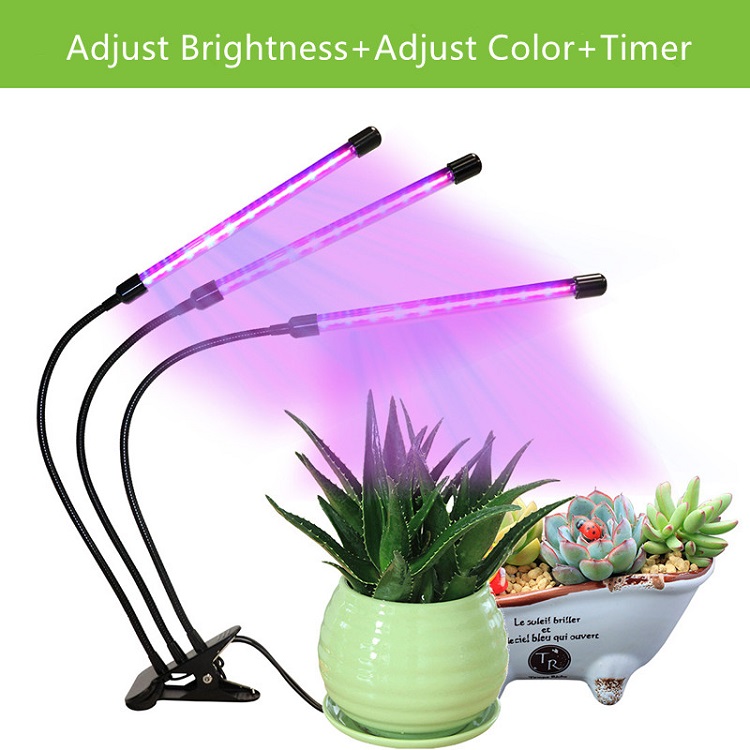
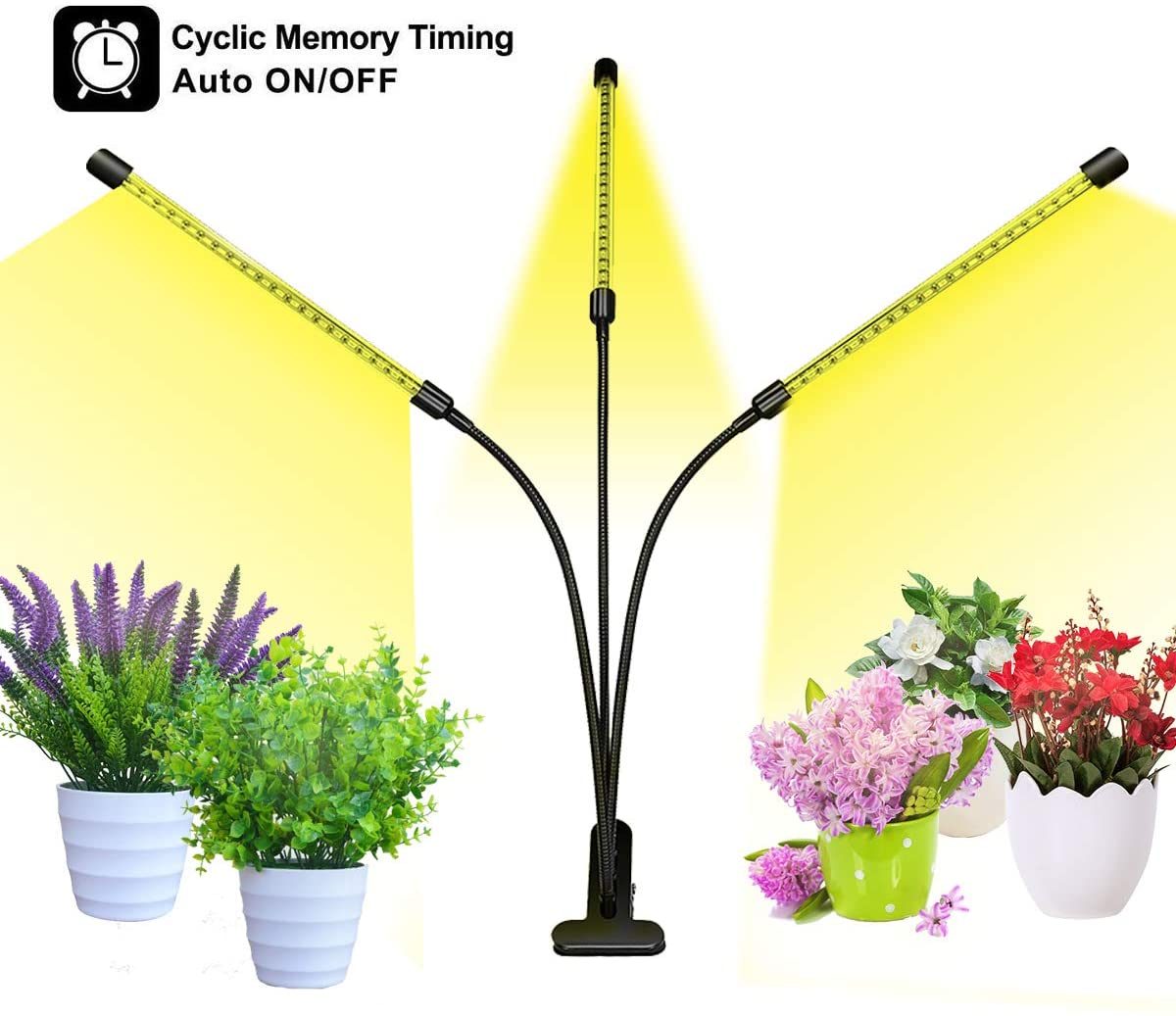
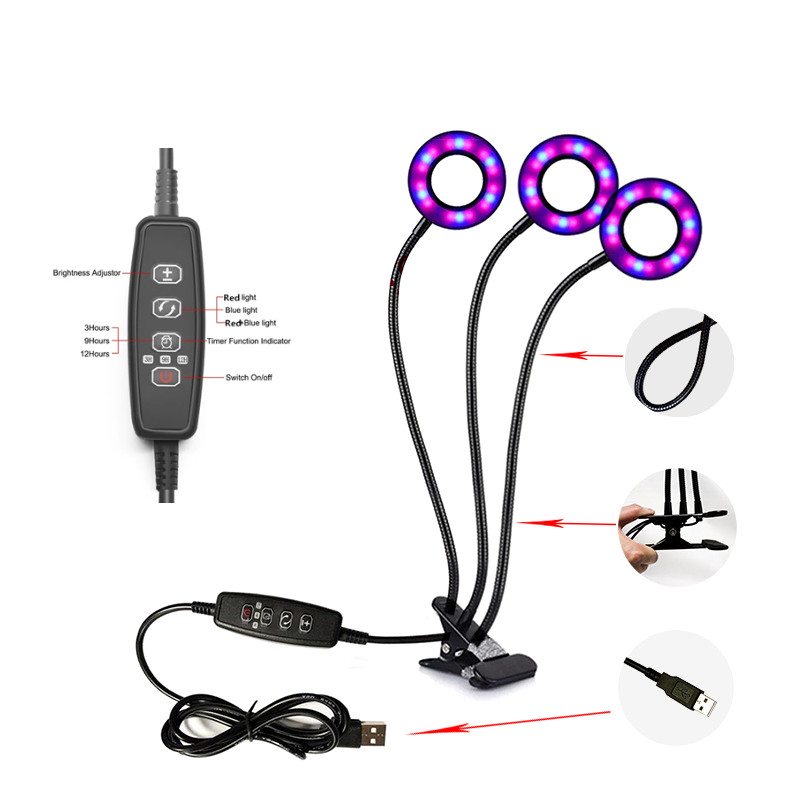
Led Grow Lights Commercial,Indoor Clamp Grow Light,Outdoor Plants Clamp Grow Light,Led Greenhouse Grow Light
Shenzhen Wenyi Lighting Technology Co., Ltd , https://www.szwenyigrow.com