Model NO.: M16
Thickness: 7mm
Customized: Customized
Trademark: MCS
Transport Package: Three Plywood
Specification: 96"x60"&96"x30"-38"
Origin: Zhangping, China
HS Code: 68101910
Model NO.: M16
Thickness: 7mm
Customized: Customized
Trademark: MCS
Transport Package: Three Plywood
Specification: 96"x60"&96"x30"-38"
Origin: Zhangping, China
HS Code: 68101910
Standard Panel System Details:
Product: Panel Systems
Series: Contemporary
Model: 6" x 24"
Pattern: Smooth, staggered block
Recommended Use: Tub and Shower Surrounds, Backsplashes
Panel Widths:30''~36'' side wall (2 pieces) ,"48''~60'' back wall (1 piece)
Height: 96'' max height
Thickness: 8mm
Finish: Gloss
6" x 24" Smooth block patter
Solid one-piece panels
Permanently sealed surface
Easy to install
Easy to maintain
Made in the China
Packaging & Delivery
Packaging Details:Plywood Crates without fumigation
Delivery Time: During 30 days after payment
CARE & MAINTENANCE
Clean with a soft sponge or cloth using an aerosol foam or spray cleaner. We recommend you clean the silicone adhesive too... this will help prevent decay and separation of the water sealant.
To maintain the brilliant luster of your cultured product, just wipe down with a bath squeegee on a regular basis.
The following mild abrasives will remove simple scratches & stains:
- Auto polishing compound,
- Gel gloss, or
- Baking soda & water
- Never use a metal scrubber, scouring powder, or harsh chemicals on your cultured marble product. For example, nail polish remover can cause permanent damage to the gel coat, and can discolor the resin material itself.
- For added protection, and increased shine, apply two coats of an automotive paste wax every year.
- Given proper care, cultured marble will provide years of problem free use, in an attractive, and affordable package.
- Care and maintenance guidelines are available in PDF format in the Downloads section.
- Â
- Â
- MANUFACTURING PROCESS
- Cast polymer manufacturing is performed in an "open mold" system, in which synthetic and natural fillers are combined with a polyester resin binder to create a composite 'matrix'. This matrix is then poured into fiberglass molds which have been pre-treated with a gel coat that provides the waterproof protection on the product's surface. After a curing process hardens the matrix within the mold, the product is removed from the mold and undergoes a detailing process.
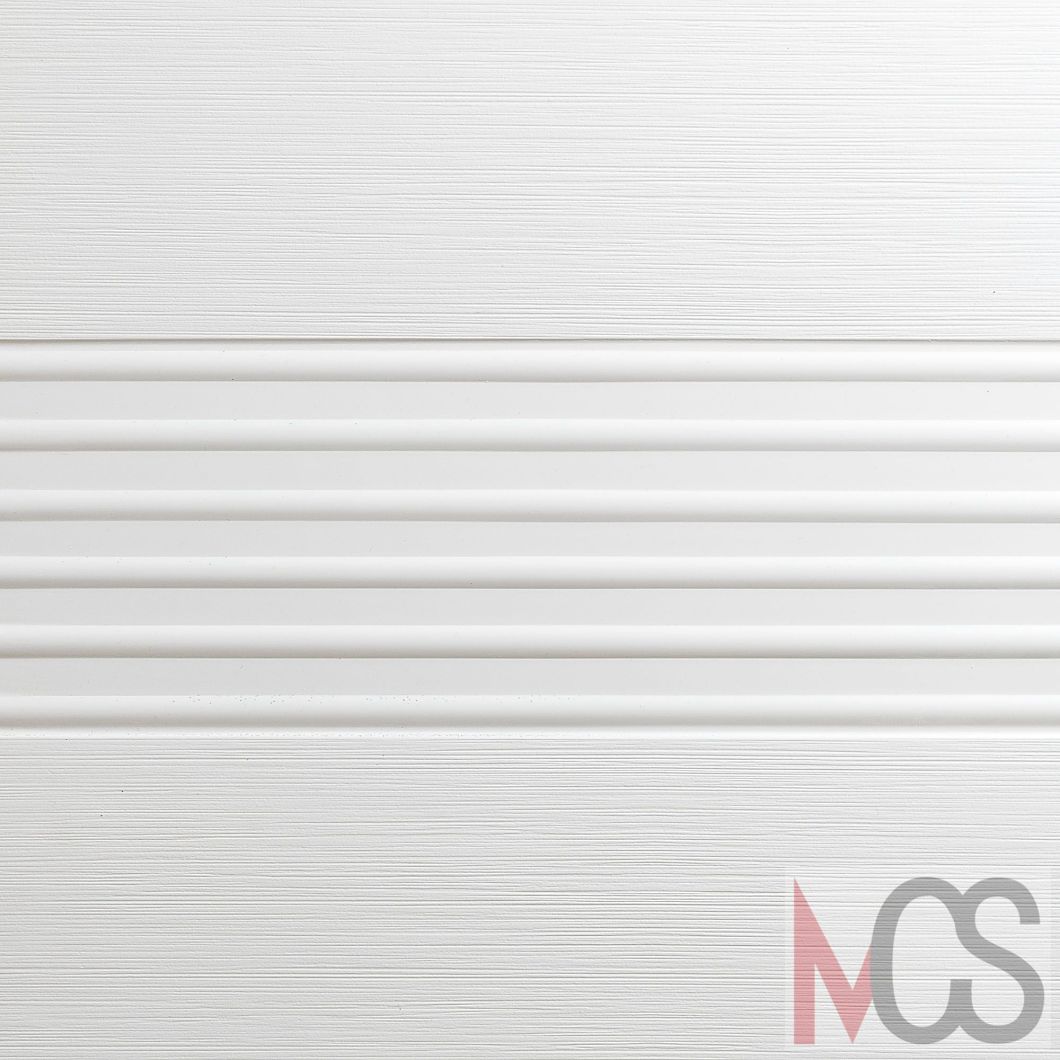
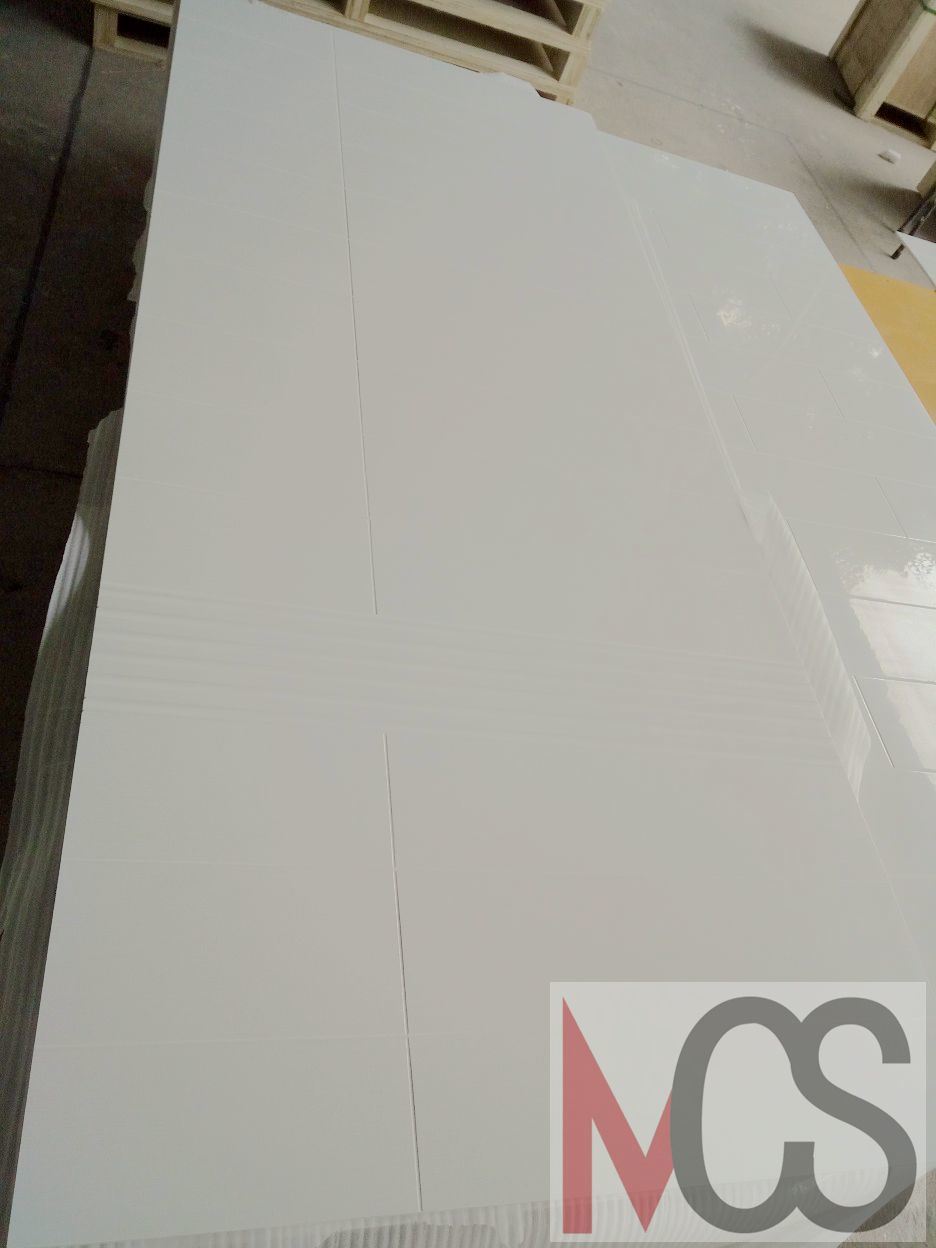
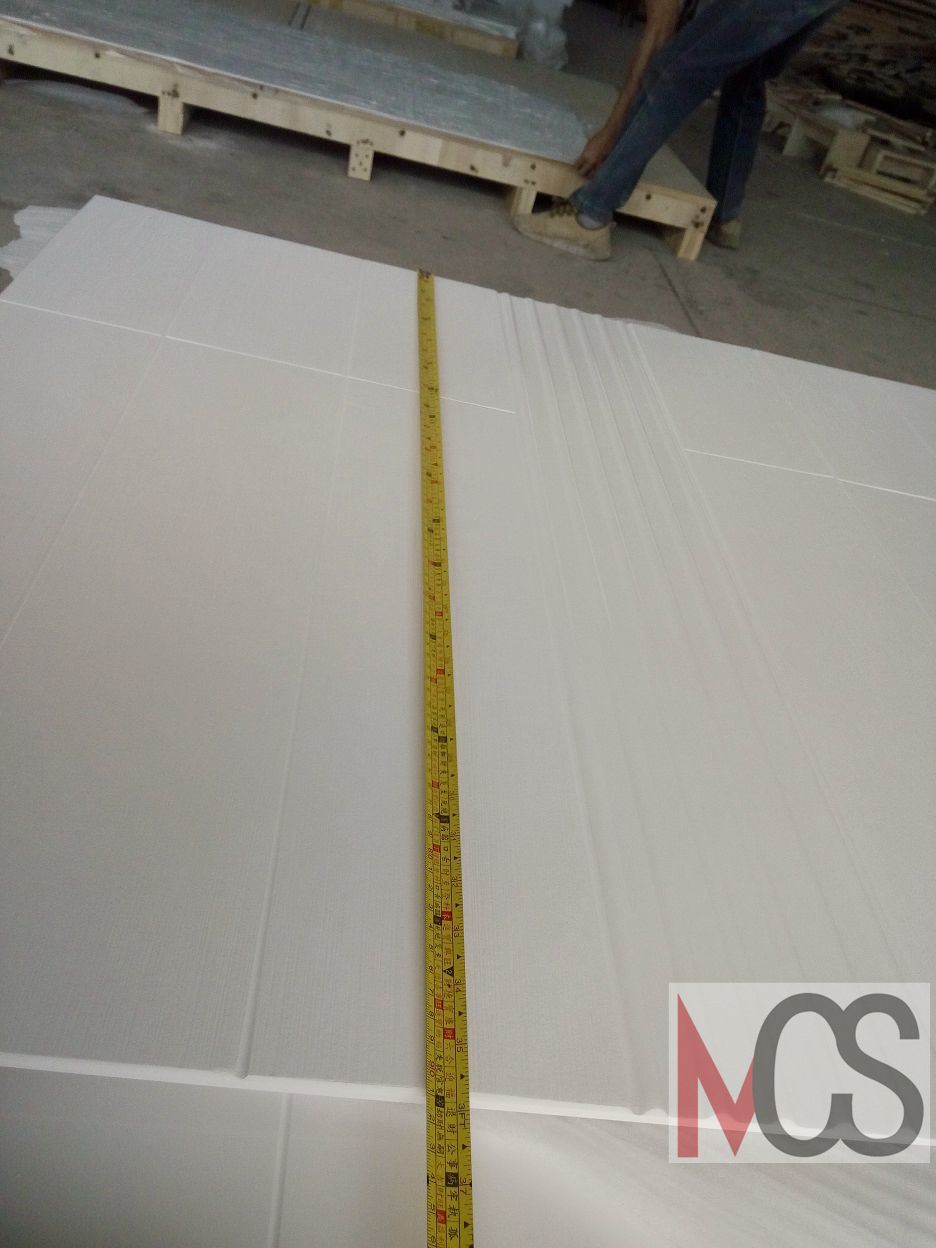
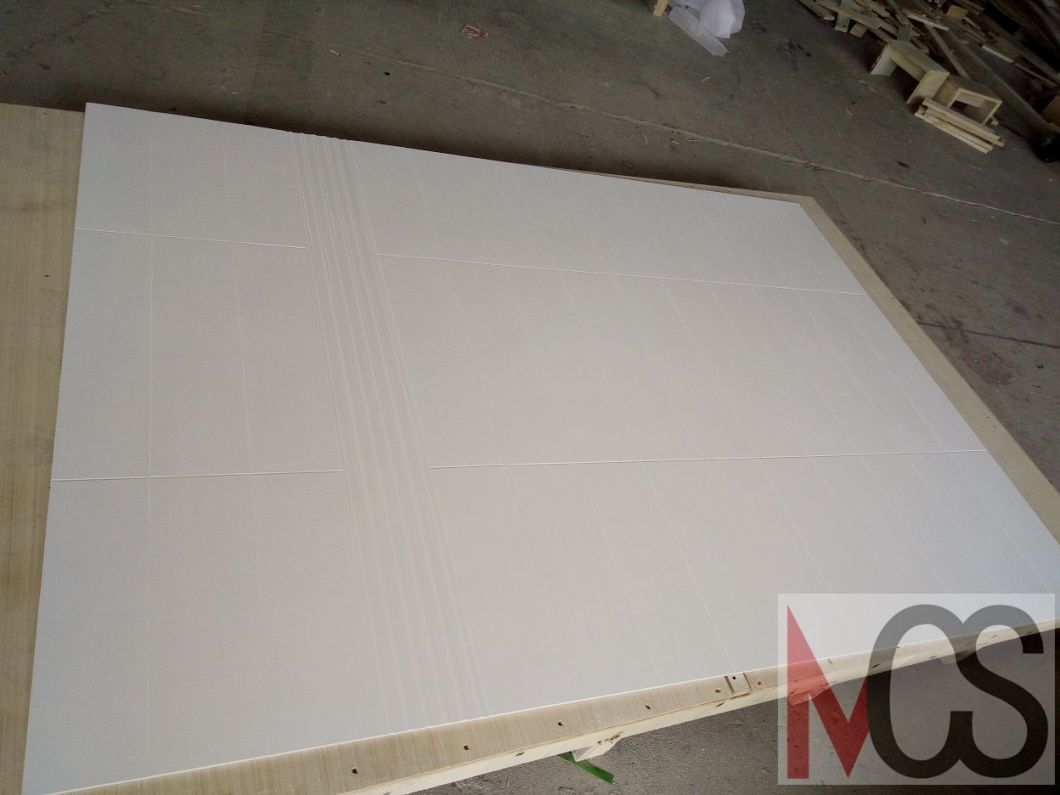
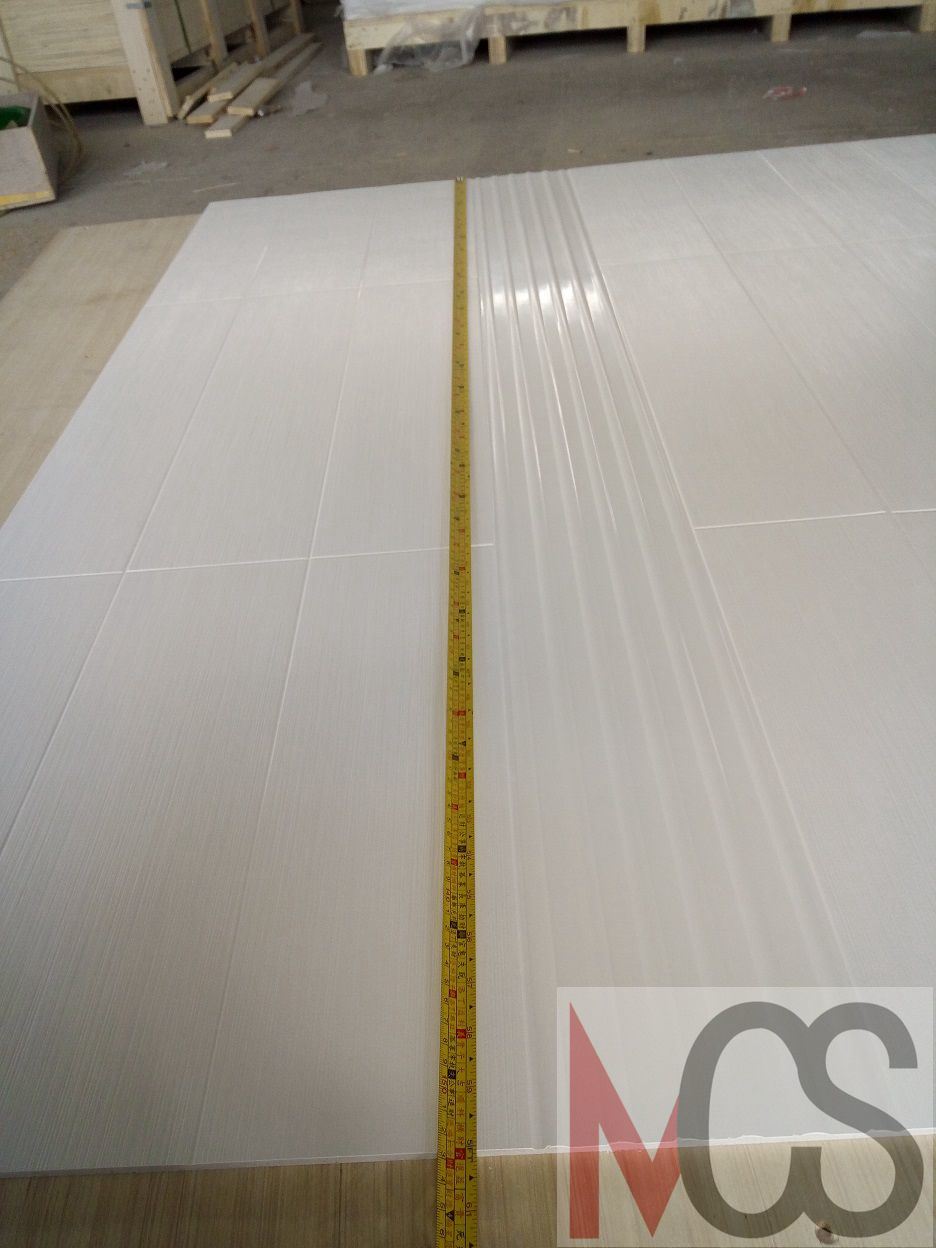
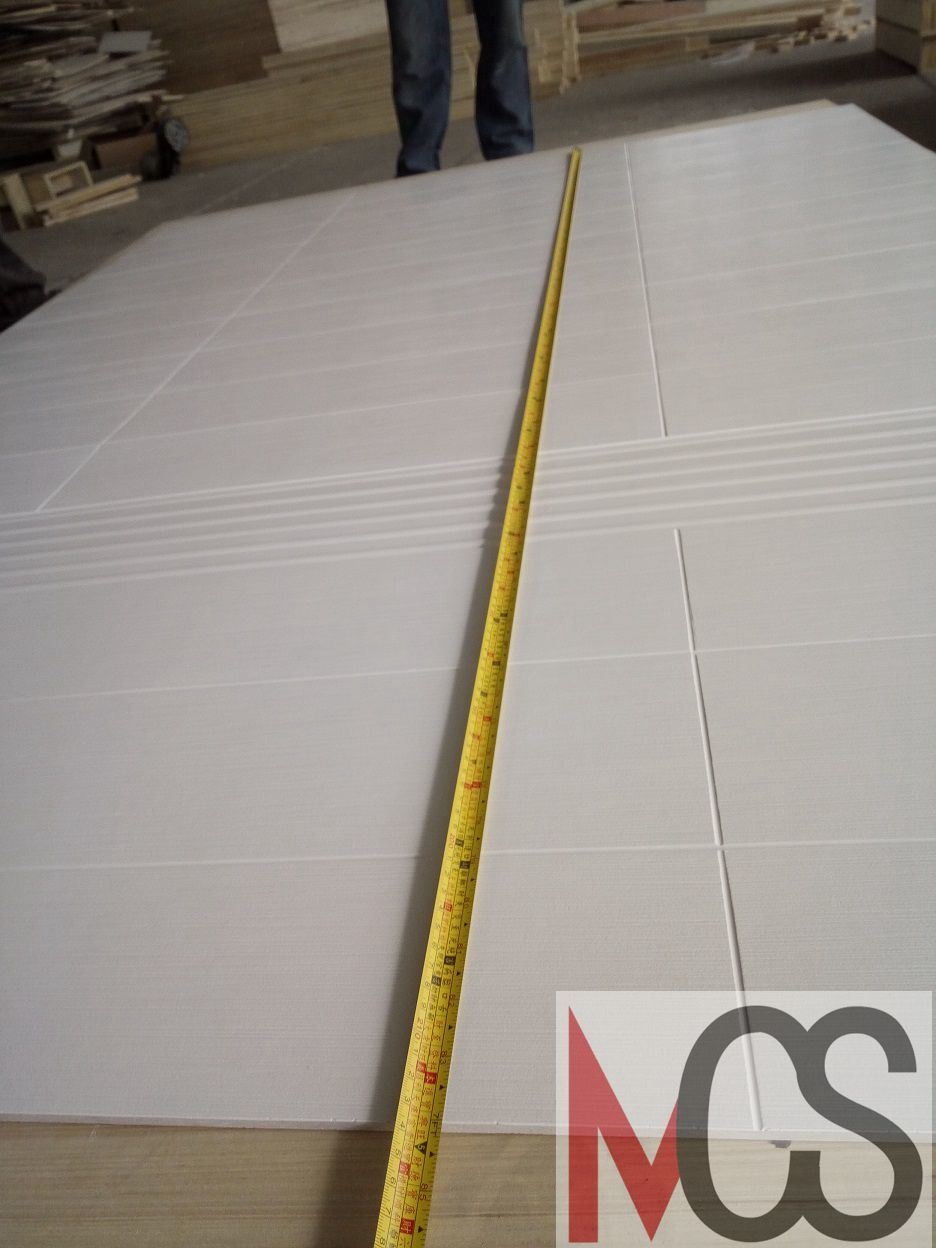
Â
Standard Panel System Details:
Product: Panel Systems
Series: Contemporary
Model: 6" x 24"
Pattern: Smooth, staggered block
Recommended Use: Tub and Shower Surrounds, Backsplashes
Panel Widths:30''~36'' side wall (2 pieces) ,"48''~60'' back wall (1 piece)
Height: 96'' max height
Thickness: 8mm
Finish: Gloss
6" x 24" Smooth block patter
Solid one-piece panels
Permanently sealed surface
Easy to install
Easy to maintain
Made in the China
Packaging & Delivery
Packaging Details:Plywood Crates without fumigation
Delivery Time: During 30 days after payment
CARE & MAINTENANCE
Clean with a soft sponge or cloth using an aerosol foam or spray cleaner. We recommend you clean the silicone adhesive too... this will help prevent decay and separation of the water sealant.
To maintain the brilliant luster of your cultured product, just wipe down with a bath squeegee on a regular basis.
The following mild abrasives will remove simple scratches & stains:
- Auto polishing compound,
- Gel gloss, or
- Baking soda & water
- Never use a metal scrubber, scouring powder, or harsh chemicals on your cultured marble product. For example, nail polish remover can cause permanent damage to the gel coat, and can discolor the resin material itself.
- For added protection, and increased shine, apply two coats of an automotive paste wax every year.
- Given proper care, cultured marble will provide years of problem free use, in an attractive, and affordable package.
- Care and maintenance guidelines are available in PDF format in the Downloads section.
- Â
- Â
- MANUFACTURING PROCESS
- Cast polymer manufacturing is performed in an "open mold" system, in which synthetic and natural fillers are combined with a polyester resin binder to create a composite 'matrix'. This matrix is then poured into fiberglass molds which have been pre-treated with a gel coat that provides the waterproof protection on the product's surface. After a curing process hardens the matrix within the mold, the product is removed from the mold and undergoes a detailing process.
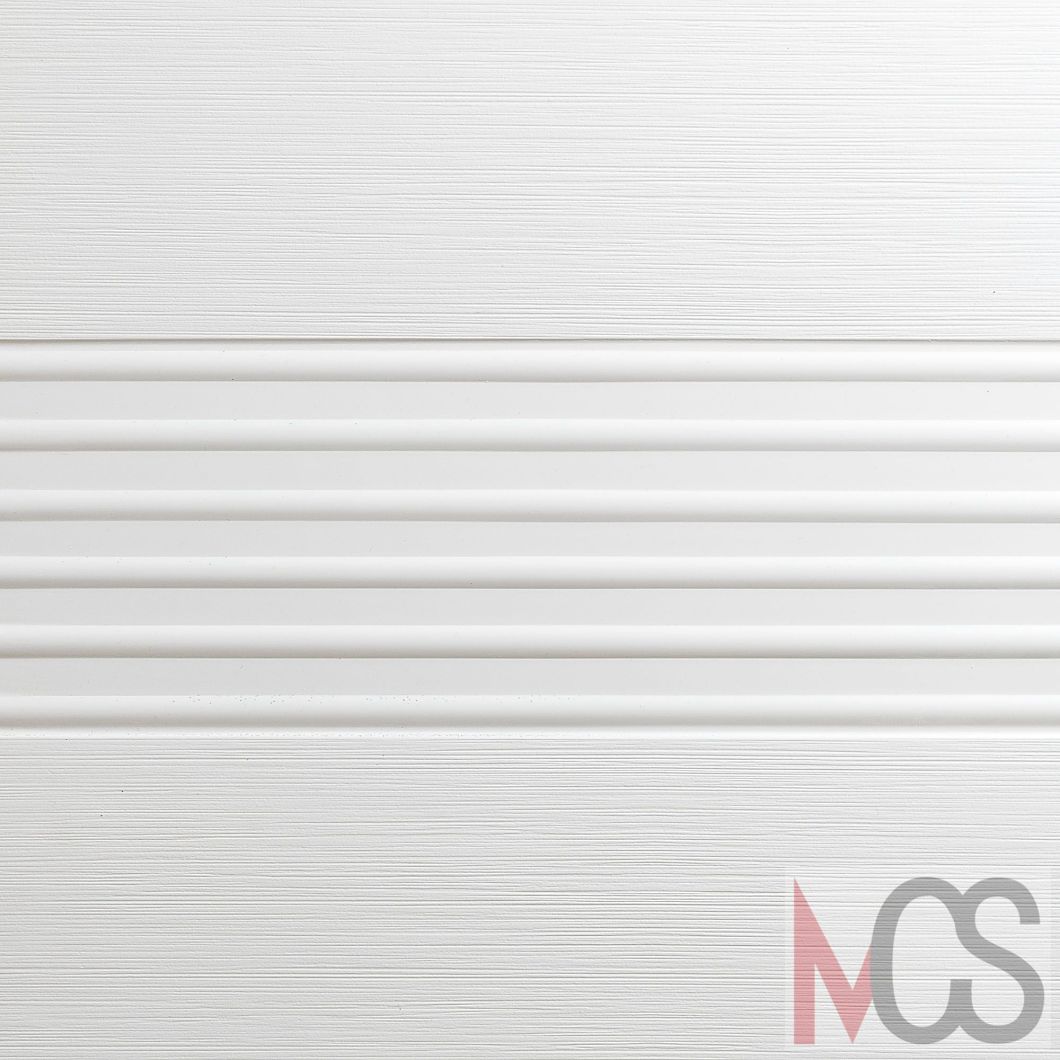
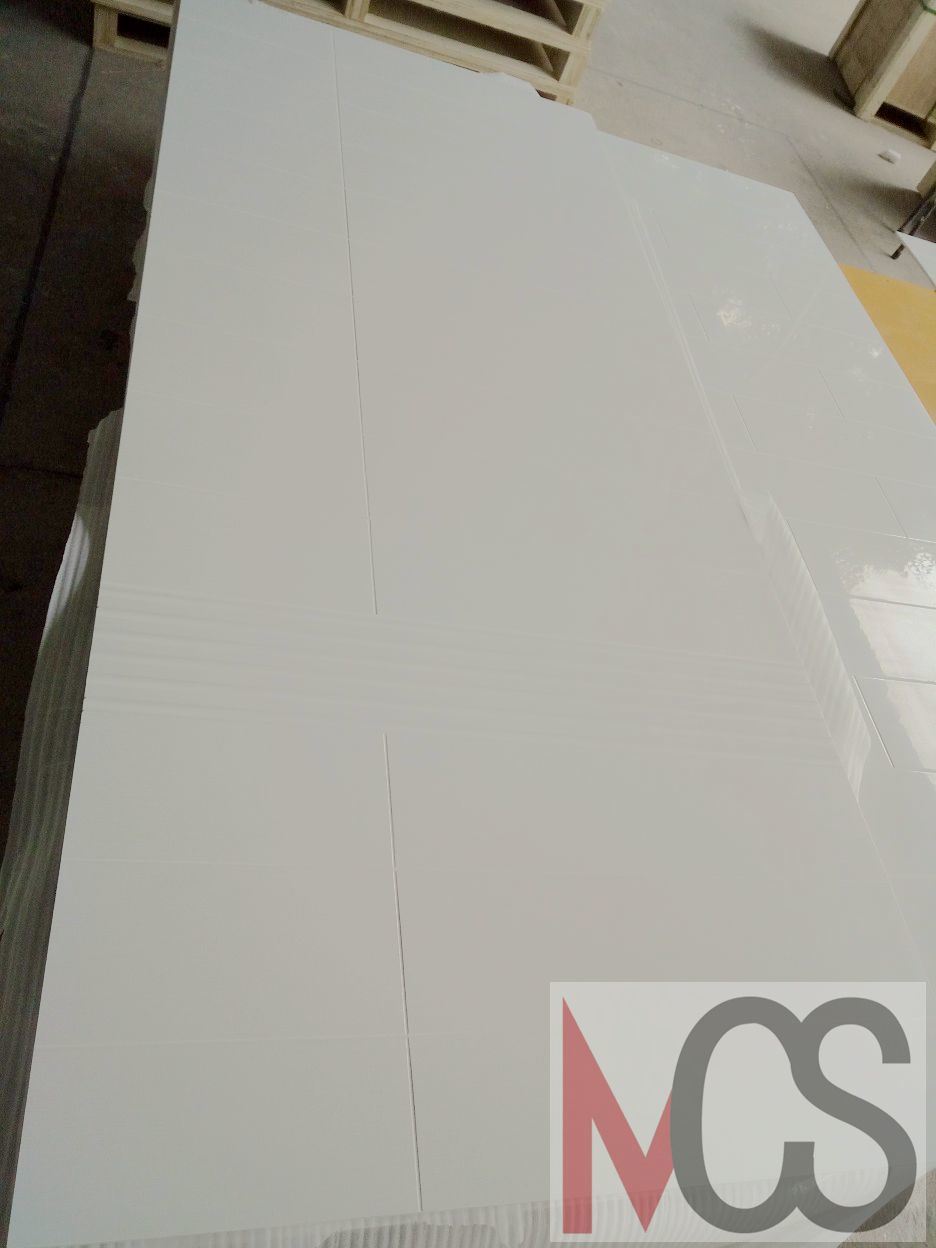
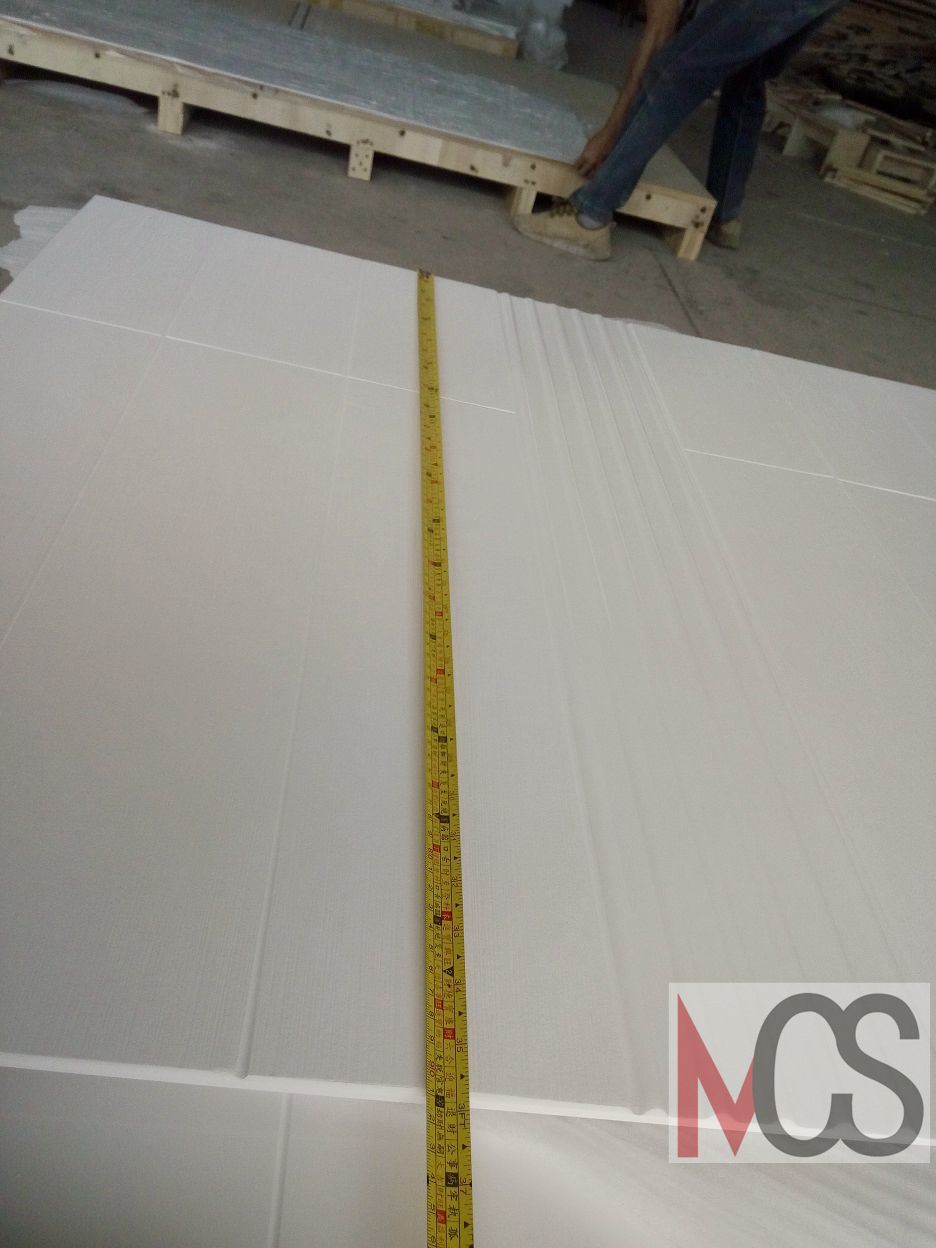
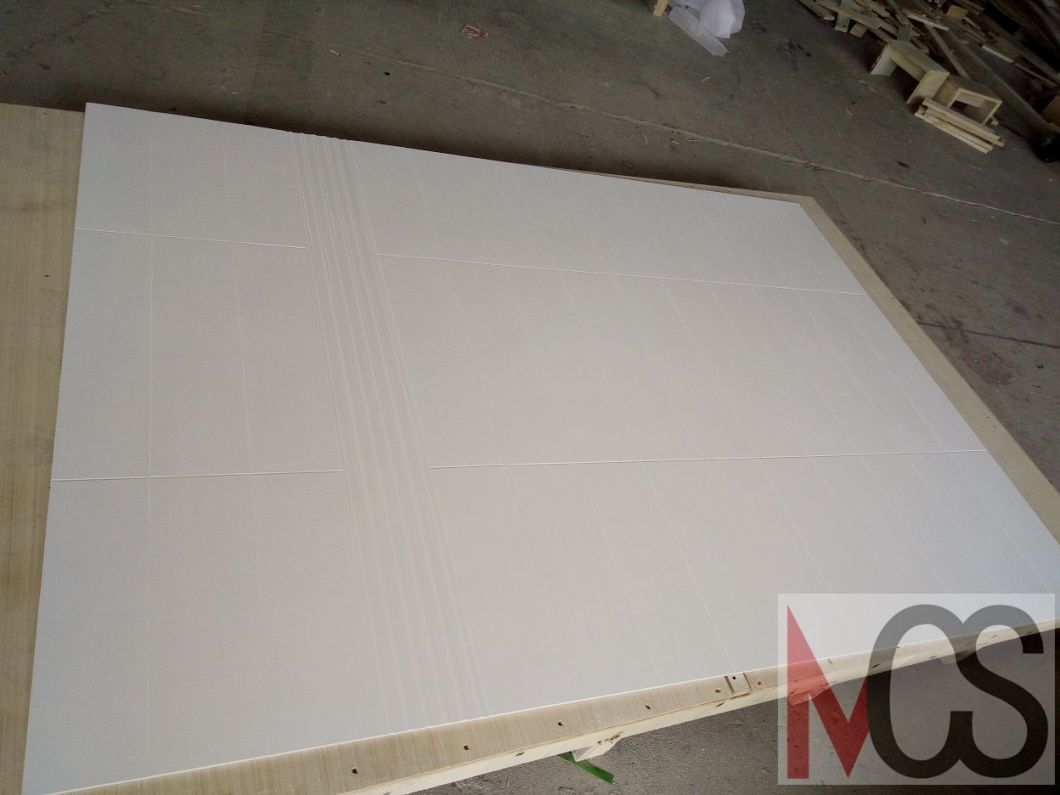
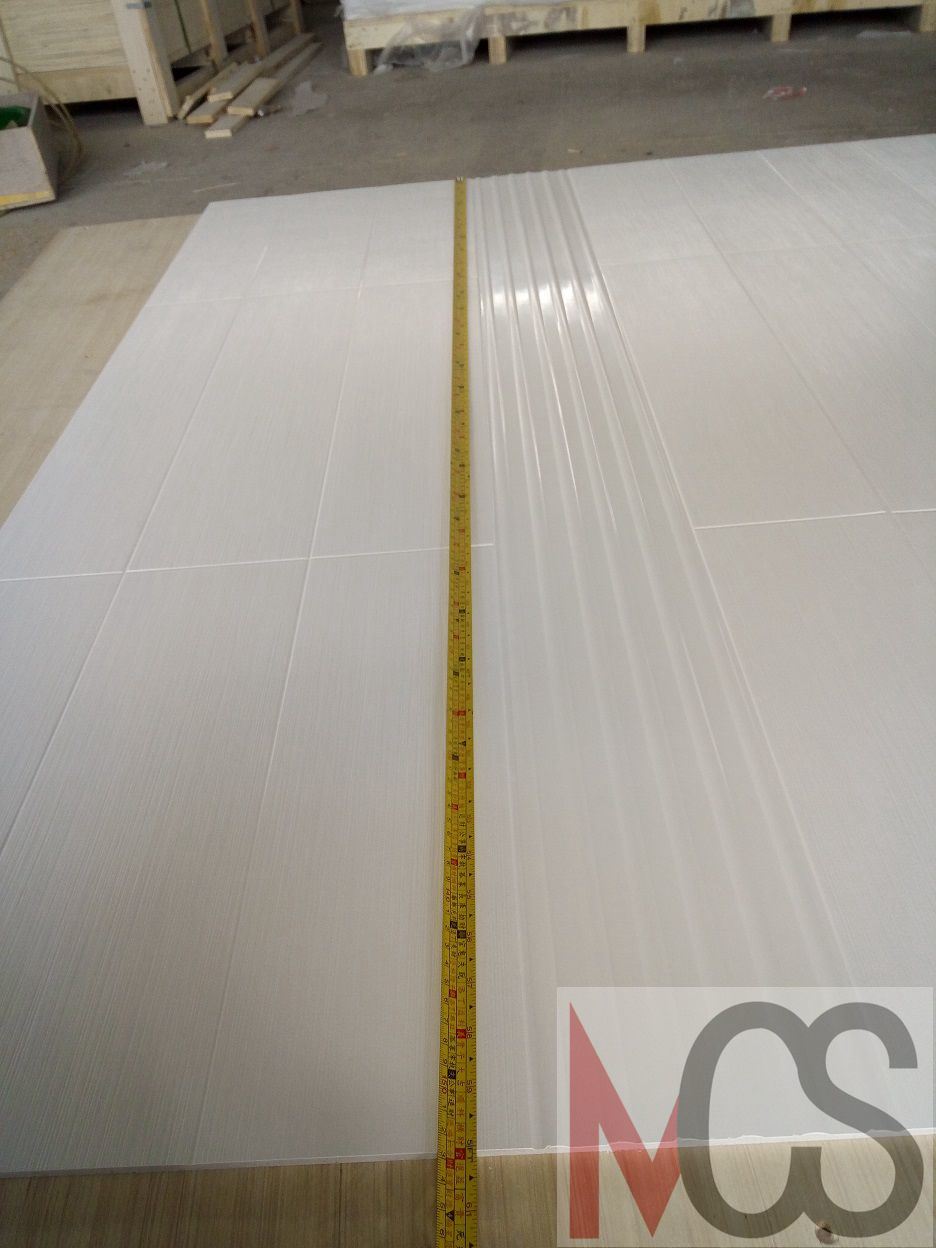
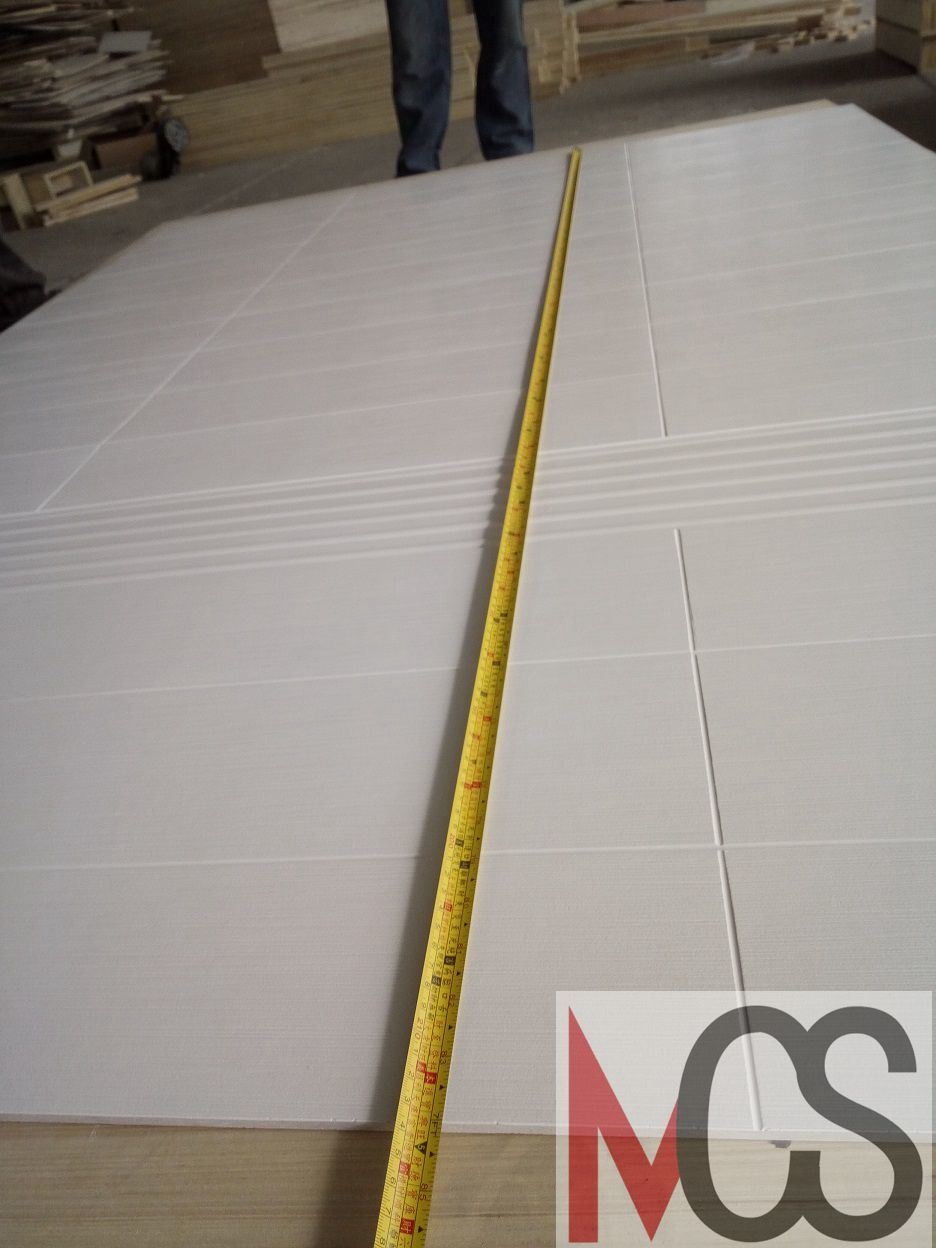
Â