Programming the measurement program in a CAM environment takes flexibility, efficiency and "completely reliable" workpiece alignment to a new level - Sikorsky supplier Alp Aviation tells you how to do this.
Alp Aviation's production engineers are not only obeying the instructions; they are also personally responsible for every aspect of the customer's parts, from raw materials to finished products. They can do this because Alp recognizes the importance of using highly flexible and efficient production methods. One of Alp's most important initiatives recently was the introduction of Renishaw's Productivity+TM software, which installed Renishaw's workpiece alignment probes in all 50 machining centers to create and test programs in a CAM environment.
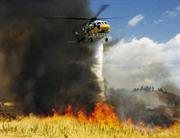
“Alp must be a technical knowledge center, and the key to doing this is the communication and relationships between employees†– General Manager Ş enay İ dil talks about how he creates a sound culture for employees to manage their processes. When you talk to an engineer, you will find that they are equally enthusiastic about the best practices – “We delve into the entire production cycle time and in some cases reduce it by 50%,†says engineering design team lead Cenk Akin. . He continued: "It is Productivity+ software and Renishaw's workpiece aligning probes that have enabled us to achieve this goal. The advantages are not only to save time and money; but also to give us complete confidence in the production process, because all machine operations The possibility of error has been eliminated and the repeatability of the production process has been improved – by using a probe with a repeatability of less than 1 micron, we have achieved a higher level of repeatability and reproducibility.
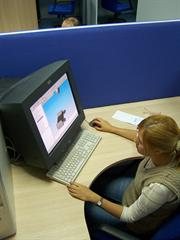
Process design process
When manufacturing new parts, the company assigns a production engineer to be responsible for all the processes in the part production cycle. The customer sends CAD data to the engineer, and the cutting process, including tool selection, is determined by the Unigraphics CAM system. The NC part program created by Unigraphics is then loaded into Renishaw's Productivity+TM software package, and the engineer adds measurement cycles to the software package. The completed program is loaded into the appropriate machine via the DNC system, and before the full production begins, the machine processes a part to test the machining and measurement procedures.
Productivity+ saves time and costs
Productivity+ was purchased in July 2007 to reduce production process development time – Alp's work environment is almost paperless and highly automated, so they cannot afford the time lost by manual measurement procedures.
Productivity+ uses a graphical user interface (GUI) to provide an extremely convenient programming environment. Alp engineers can define a program by simply selecting the workpiece features from the CAD model or by selecting parameters from the dialog box. Once the program definition is complete, you can load the program directly into the machine by selecting the required post-processor and automatically generating the output.
To be more reliable, the measurement cycle can be simulated on a computer and all errors are indicated before the probe is mounted on the machine. The engineering team leader, Cenk Akin, explained the main benefits that the software brings to Alp: "Productivity+ makes it easier to verify the process before machine production. If the machine is only used to test the process, not to produce parts that can be sold, Then we are wasting money."
Probe for workpiece alignment and in-sequence detection
Alp Aviation uses probes in the machining cycle
Productivity+ is a recently purchased product from Alp, but for many years Alp has been using Renishaw's spindle-mounted workpiece alignment probes – all new machines are equipped with a probe system. Engineers still remember the fact that Alp had purchased the Renishaw probe before – “The operator manually adjusted the parts on the workbench, or we made an expensive one for each part variant. Special fixtures. It is crucial to change these manual alignment methods – this is a torture for the operator!
Now the operator uses a simple fixture, we program the machine and use the probe to position the part. The probe is also used in the subsequent stages of the process. For example, each workpiece is inspected prior to finishing and tested at the completion of the machining. In some cases the production cycle time has been reduced by as much as 50%.
Another important feature is that the measurement program automatically updates the machine offset value. In the past we relied on operators, and they were very error-prone – this simple feature avoided many scraps. Accuracy is also improved – we regularly cross-check the probe measurements with a hand gauge, and typically our measurement repeatability error can be less than 1 micron. â€
Reducing the auxiliary time is especially important for Alp because they produce a variety of parts and have a strong need for flexibility. Some batches can be produced on the machine for one year, but some machines change two or three batches per day, with only a few parts per batch. Particularly impressive is that Alp is close to their goal of zero-positive time. The use of the exchange table system allows the operator to load other workpieces while machining one workpiece, while the probe system can be within seconds. Finish the workpiece alignment.
Alp Aviation's philosophy
Alp General Manager Alp General Manager Ş enay İ dil explained the company's way of doing business – “We don't undertake general processing work, nor what parts are processed by airlines. We carefully select customers to build long-term relationships. This is because we believe that the work we are familiar with can last long, so strategic development planning is part of our work.
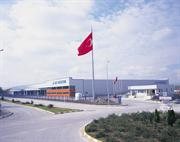
We use this long-term cooperation strategy for our customers and suppliers. The technology we are talking about today, Renishaw's probe system and Productivity+ software, is important for this strategy – investing at the lowest cost necessary to ensure that the machine is operating as efficiently as possible. After careful consideration in 2006, we invested $12.5 million to purchase machine tools and other systems, but I hope that each machine is equipped with a probe system. We determined the exact machine specifications and we even asked them to make a special extended table machine that was not available in the Mazak series and purchased the first machine they built.
Alp Aviation's typical assembly quality is an essential element in the production of aerospace parts. According to the definition of the production engineer, dimensional control is carried out in the sequence and all contour features of the finished product are independently checked.
Ball Valves
Ball Valves,Flange Type Ball Valve,Flanged Ball Valve,Platform Flanged Ball Valve
ZHITONG PIPE VALVE TECHNOLOGY CO.,LTD , https://www.ztongvalve.com